Budowa maszyn produkcyjnych to złożony proces, który wymaga uwzględnienia wielu kluczowych elementów. W pierwszej kolejności należy zwrócić uwagę na konstrukcję mechaniczną, która jest fundamentem każdej maszyny. Obejmuje ona ramę, podzespoły oraz elementy nośne, które muszą być odpowiednio zaprojektowane, aby zapewnić stabilność i wytrzymałość. Kolejnym istotnym aspektem jest system napędowy, który może obejmować silniki elektryczne, hydrauliczne lub pneumatyczne. Wybór odpowiedniego napędu ma kluczowe znaczenie dla efektywności działania maszyny. Dodatkowo, nie można zapominać o systemach sterowania, które umożliwiają precyzyjne zarządzanie pracą maszyny. W nowoczesnych rozwiązaniach często wykorzystywane są systemy automatyki oraz programowalne sterowniki logiczne (PLC), które zwiększają wydajność i elastyczność produkcji. Warto również wspomnieć o materiałach, z jakich wykonane są poszczególne komponenty maszyny. Muszą one charakteryzować się odpowiednią odpornością na zużycie oraz korozję, co wpływa na długowieczność urządzenia.
Jakie technologie są wykorzystywane w budowie maszyn produkcyjnych
W dzisiejszych czasach budowa maszyn produkcyjnych opiera się na zaawansowanych technologiach, które znacznie zwiększają ich wydajność oraz precyzję działania. Jedną z najważniejszych technologii jest CAD, czyli komputerowe wspomaganie projektowania, które pozwala inżynierom na tworzenie szczegółowych modeli 3D maszyn przed ich fizycznym wytworzeniem. Dzięki temu możliwe jest przeprowadzenie symulacji i analiz, co minimalizuje ryzyko błędów w późniejszym etapie produkcji. Inną istotną technologią jest CAM, czyli komputerowe wspomaganie wytwarzania, które automatyzuje procesy obróbcze i montażowe. Wykorzystanie robotów przemysłowych stało się standardem w wielu zakładach produkcyjnych, co przyczynia się do zwiększenia efektywności i redukcji kosztów pracy. Ponadto technologie druku 3D zaczynają odgrywać coraz większą rolę w budowie maszyn produkcyjnych, umożliwiając szybkie prototypowanie oraz produkcję skomplikowanych komponentów bez potrzeby stosowania tradycyjnych metod wytwarzania.
Jakie są najczęstsze problemy w budowie maszyn produkcyjnych
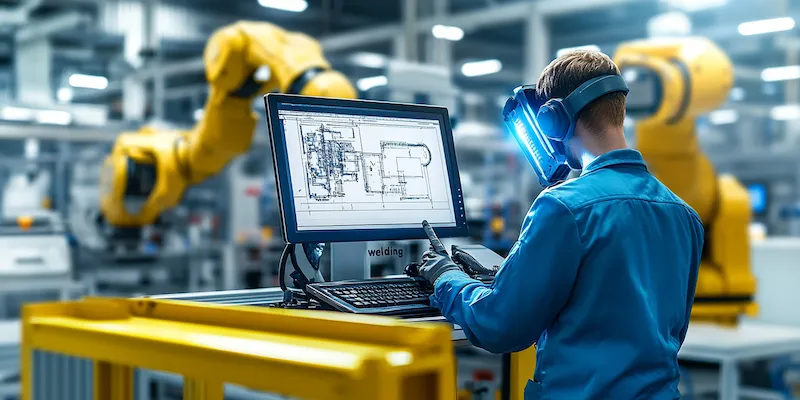
Budowa maszyn produkcyjnych wiąże się z wieloma wyzwaniami i problemami, które mogą wpłynąć na jakość końcowego produktu oraz efektywność całego procesu produkcji. Jednym z najczęstszych problemów jest niewłaściwe dobranie materiałów do konstrukcji maszyny. Użycie materiałów o niewystarczającej wytrzymałości lub odporności na zużycie może prowadzić do szybkiego uszkodzenia komponentów i konieczności ich wymiany. Kolejnym istotnym zagadnieniem są błędy projektowe, które mogą wynikać z niedostatecznej analizy wymagań technicznych lub braku doświadczenia zespołu projektowego. Takie błędy mogą prowadzić do poważnych awarii podczas eksploatacji maszyny. Również problemy związane z integracją różnych systemów sterowania mogą powodować zakłócenia w pracy maszyny oraz obniżać jej wydajność. Dodatkowo, nieodpowiednia konserwacja i serwisowanie maszyn mogą prowadzić do ich przedwczesnego zużycia oraz zwiększać ryzyko awarii.
Jakie są przyszłe kierunki rozwoju budowy maszyn produkcyjnych
Przyszłość budowy maszyn produkcyjnych zapowiada się niezwykle interesująco dzięki dynamicznemu rozwojowi technologii oraz zmieniającym się potrzebom rynku. Jednym z kluczowych kierunków rozwoju będzie dalsza automatyzacja procesów produkcyjnych. W miarę jak technologia robotyczna staje się coraz bardziej zaawansowana i dostępna, więcej przedsiębiorstw zdecyduje się na wdrożenie robotów do swoich linii produkcyjnych w celu zwiększenia wydajności i redukcji kosztów pracy. Równocześnie rozwój sztucznej inteligencji pozwoli na bardziej inteligentne zarządzanie procesami produkcyjnymi poprzez analizę danych oraz uczenie maszynowe. Kolejnym istotnym trendem będzie personalizacja produktów, co wymusi na producentach elastyczność w projektowaniu maszyn zdolnych do realizacji indywidualnych zamówień klientów. W kontekście ochrony środowiska można zauważyć rosnącą tendencję do projektowania maszyn energooszczędnych oraz wykorzystujących odnawialne źródła energii. Przemysł 4.0 staje się rzeczywistością dzięki integracji technologii IoT oraz big data w procesach produkcyjnych, co umożliwi lepsze monitorowanie i optymalizację pracy maszyn.
Jakie są kluczowe etapy w budowie maszyn produkcyjnych
Budowa maszyn produkcyjnych to proces, który można podzielić na kilka kluczowych etapów, z których każdy odgrywa istotną rolę w osiągnięciu końcowego celu. Pierwszym krokiem jest faza koncepcyjna, w której określane są wymagania dotyczące maszyny oraz jej funkcjonalności. Na tym etapie inżynierowie i projektanci współpracują z klientami, aby zrozumieć ich potrzeby oraz oczekiwania. Następnie następuje faza projektowania, w której tworzone są szczegółowe rysunki techniczne oraz modele 3D. Wykorzystanie nowoczesnych narzędzi CAD pozwala na dokładne odwzorowanie wszystkich elementów maszyny oraz przeprowadzenie symulacji działania. Po zakończeniu projektowania przystępuje się do fazy prototypowania, gdzie powstaje pierwsza wersja maszyny. To kluczowy moment, ponieważ pozwala na testowanie rozwiązań oraz identyfikację potencjalnych problemów przed rozpoczęciem masowej produkcji. Kolejnym etapem jest produkcja, która obejmuje wytwarzanie poszczególnych komponentów oraz ich montaż. W tej fazie niezwykle ważne jest zapewnienie wysokiej jakości materiałów oraz precyzyjnego wykonania. Po zakończeniu montażu maszyna przechodzi przez testy wydajnościowe i bezpieczeństwa, które mają na celu potwierdzenie jej zgodności z wymaganiami technicznymi.
Jakie są najważniejsze normy i standardy w budowie maszyn produkcyjnych
W budowie maszyn produkcyjnych niezwykle istotne jest przestrzeganie odpowiednich norm i standardów, które mają na celu zapewnienie bezpieczeństwa użytkowników oraz wysokiej jakości produktów. W Europie jednym z najważniejszych dokumentów regulujących kwestie związane z bezpieczeństwem maszyn jest dyrektywa maszynowa 2006/42/WE. Określa ona wymagania dotyczące projektowania, budowy i eksploatacji maszyn, a także zasady oceny zgodności. Przemysłowcy muszą również zwracać uwagę na normy ISO, które dotyczą różnych aspektów budowy maszyn, takich jak jakość materiałów czy efektywność energetyczna. Normy te są szczególnie ważne w kontekście globalizacji rynku, ponieważ zapewniają jednolite standardy dla producentów działających na różnych rynkach. Dodatkowo, certyfikaty takie jak CE są niezbędne do legalnego wprowadzenia maszyny na rynek europejski. Warto również wspomnieć o normach dotyczących ochrony środowiska, które stają się coraz bardziej istotne w kontekście zrównoważonego rozwoju przemysłu.
Jakie umiejętności są potrzebne do pracy przy budowie maszyn produkcyjnych
Praca przy budowie maszyn produkcyjnych wymaga szerokiego zakresu umiejętności oraz wiedzy technicznej. Kluczowym aspektem jest znajomość zasad inżynierii mechanicznej, która obejmuje zarówno teorię, jak i praktykę dotyczącą projektowania i wytwarzania maszyn. Osoby pracujące w tej branży powinny być dobrze zaznajomione z programami CAD oraz CAM, które umożliwiają tworzenie modeli 3D i automatyzację procesów produkcyjnych. Umiejętność analizy danych oraz rozwiązywania problemów technicznych jest równie ważna, ponieważ często pojawiają się sytuacje wymagające szybkiego podejmowania decyzji w obliczu awarii lub nieprawidłowego działania maszyny. Dodatkowo, znajomość systemów automatyki oraz programowania PLC staje się coraz bardziej pożądana w kontekście nowoczesnych rozwiązań przemysłowych. Komunikacja interpersonalna również odgrywa istotną rolę, ponieważ praca nad projektem często wymaga współpracy z innymi specjalistami z różnych dziedzin, takich jak elektronika czy informatyka. Nie można zapominać o umiejętnościach manualnych i technicznych, które są niezbędne podczas montażu i konserwacji maszyn.
Jakie są zalety stosowania nowoczesnych technologii w budowie maszyn produkcyjnych
Stosowanie nowoczesnych technologii w budowie maszyn produkcyjnych przynosi wiele korzyści zarówno dla producentów, jak i dla użytkowników końcowych. Przede wszystkim technologie te pozwalają na zwiększenie efektywności procesów produkcyjnych poprzez automatyzację wielu czynności. Robotyzacja linii produkcyjnych prowadzi do znacznego skrócenia czasu realizacji zamówień oraz redukcji kosztów pracy. Ponadto nowoczesne technologie umożliwiają lepszą kontrolę jakości produktów dzięki zastosowaniu zaawansowanych systemów monitorujących oraz analitycznych. Dzięki nim możliwe jest szybkie wykrywanie błędów i nieprawidłowości w procesie produkcji, co wpływa na poprawę ogólnej jakości wyrobów. Również zastosowanie technologii IoT pozwala na zbieranie danych z różnych etapów produkcji, co umożliwia ich analizę i optymalizację procesów w czasie rzeczywistym. Dodatkowo nowoczesne technologie przyczyniają się do zmniejszenia negatywnego wpływu na środowisko poprzez zastosowanie energooszczędnych rozwiązań oraz materiałów ekologicznych. Z perspektywy użytkowników końcowych nowoczesne maszyny charakteryzują się większą niezawodnością oraz łatwiejszą obsługą dzięki intuicyjnym interfejsom użytkownika i systemom diagnostycznym.
Jakie są trendy w projektowaniu maszyn produkcyjnych
Trendy w projektowaniu maszyn produkcyjnych ewoluują wraz z postępem technologicznym oraz zmieniającymi się potrzebami rynku. Jednym z najważniejszych kierunków rozwoju jest dążenie do większej elastyczności urządzeń produkcyjnych. Współczesne zakłady przemysłowe muszą być zdolne do szybkiego dostosowywania się do zmieniających się wymagań klientów oraz różnorodności produktów. Dlatego projektanci coraz częściej wykorzystują modułowe podejście do konstrukcji maszyn, co pozwala na łatwą modyfikację i rozbudowę istniejących linii produkcyjnych bez konieczności ich całkowitej wymiany. Innym istotnym trendem jest integracja technologii cyfrowych z tradycyjnymi procesami produkcyjnymi. Wprowadzenie elementów sztucznej inteligencji oraz uczenia maszynowego umożliwia automatyczne dostosowywanie parametrów pracy maszyny do aktualnych warunków produkcji, co zwiększa efektywność i jakość wyrobów. Również rosnąca świadomość ekologiczna wpływa na projektowanie maszyn – producenci starają się tworzyć urządzenia bardziej przyjazne dla środowiska poprzez zastosowanie materiałów odnawialnych oraz energooszczędnych rozwiązań technologicznych.