Destylacja rozpuszczalników to proces, który polega na oddzieleniu składników mieszaniny na podstawie różnicy ich temperatur wrzenia. Jest to jedna z najstarszych i najbardziej powszechnie stosowanych metod separacji substancji chemicznych. Proces ten opiera się na wykorzystaniu właściwości fizycznych cieczy, a także na ich zdolności do przechodzenia w stan gazowy. W praktyce destylacja może być stosowana w różnych dziedzinach, takich jak przemysł chemiczny, farmaceutyczny czy petrochemiczny. Kluczowym elementem tego procesu jest kolumna destylacyjna, która umożliwia wielokrotne skraplanie i parowanie, co prowadzi do uzyskania wyższej czystości produktu końcowego. Warto również zwrócić uwagę na znaczenie odpowiedniego doboru warunków operacyjnych, takich jak temperatura i ciśnienie, które mają kluczowy wpływ na efektywność separacji.
Jakie są różne metody destylacji rozpuszczalników
W kontekście destylacji rozpuszczalników istnieje wiele różnych metod, które można zastosować w zależności od charakterystyki separowanej mieszaniny oraz pożądanej czystości produktu. Najpopularniejsze z nich to destylacja prosta, frakcyjna oraz destylacja pod ciśnieniem atmosferycznym lub w próżni. Destylacja prosta jest najprostszą formą tego procesu i znajduje zastosowanie w przypadku jednofazowych mieszanin o znacznej różnicy temperatur wrzenia. Z kolei destylacja frakcyjna pozwala na bardziej skomplikowane separacje, gdzie składniki mają zbliżone temperatury wrzenia. W tym przypadku wykorzystuje się kolumny frakcyjne, które umożliwiają wielokrotne skraplanie i parowanie. Destylacja pod ciśnieniem atmosferycznym jest stosowana głównie w przemyśle chemicznym, natomiast destylacja w próżni pozwala na obniżenie temperatury wrzenia substancji, co jest szczególnie przydatne w przypadku termolabilnych związków chemicznych.
Jakie są zastosowania destylacji rozpuszczalników w przemyśle
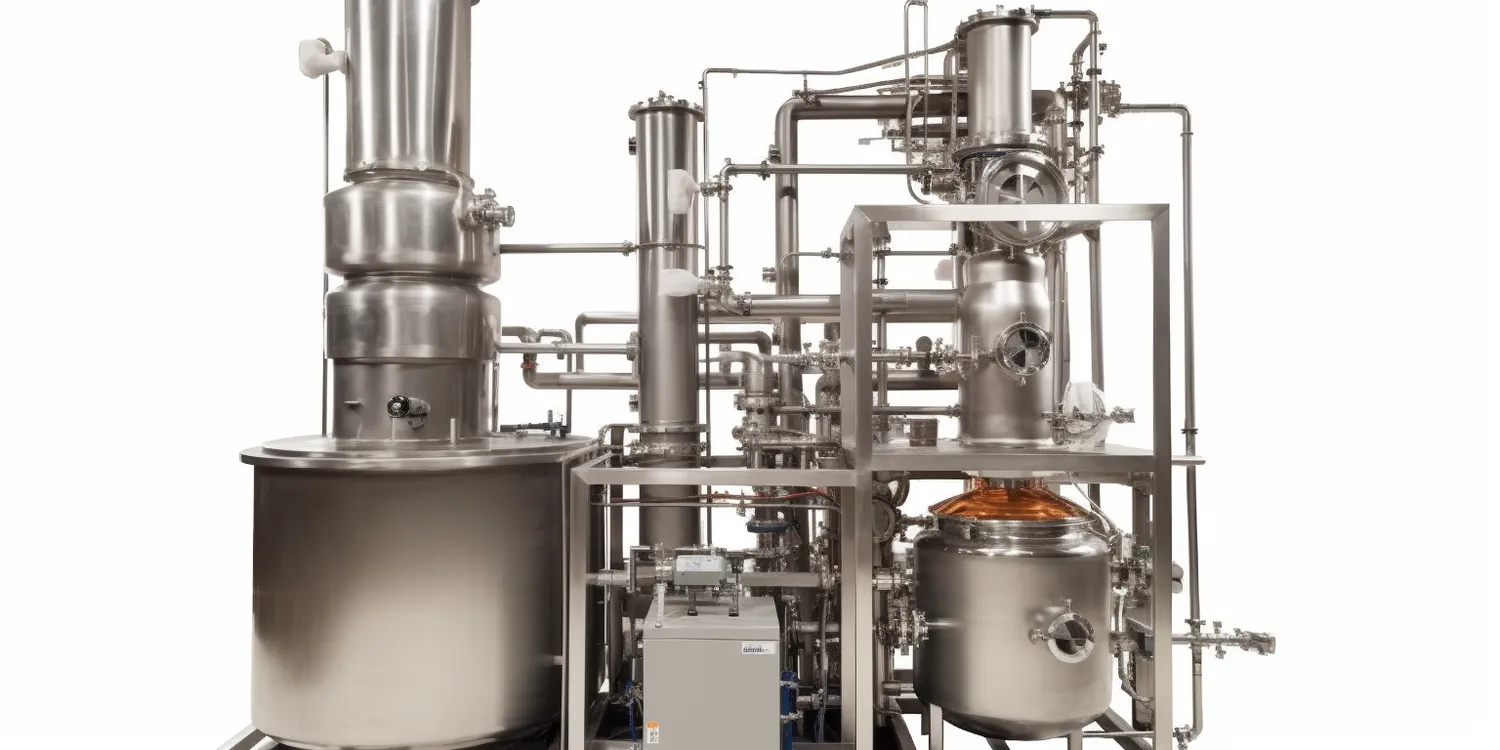
Destylacja rozpuszczalników ma szerokie zastosowanie w różnych gałęziach przemysłu, co czyni ją niezwykle istotnym procesem technologicznym. W przemyśle chemicznym wykorzystuje się ją do oczyszczania surowców oraz produktów końcowych, a także do odzyskiwania cennych substancji z odpadów. Na przykład w produkcji alkoholi etylowych proces ten pozwala na uzyskanie wysokiej czystości trunków poprzez usunięcie niepożądanych zanieczyszczeń. W przemyśle farmaceutycznym destylacja jest kluczowym etapem w produkcji leków, gdzie wymagana jest wysoka jakość i czystość substancji czynnych. Ponadto, w branży petrochemicznej proces ten jest niezbędny do separacji różnych frakcji ropy naftowej, co umożliwia produkcję paliw oraz innych produktów chemicznych.
Jakie są zalety i ograniczenia destylacji rozpuszczalników
Destylacja rozpuszczalników niesie ze sobą wiele korzyści, ale także pewne ograniczenia, które warto mieć na uwadze przy wyborze tej metody separacji. Do głównych zalet należy możliwość uzyskania wysokiej czystości produktów końcowych oraz efektywność procesu w przypadku dużych ilości materiału. Dodatkowo destylacja jest techniką stosunkowo prostą do zautomatyzowania i skalowania, co sprawia, że może być wykorzystywana zarówno w małych laboratoriach, jak i dużych zakładach przemysłowych. Niemniej jednak istnieją również pewne ograniczenia związane z tym procesem. Przede wszystkim skuteczność destylacji zależy od różnicy temperatur wrzenia składników mieszaniny; jeśli ta różnica jest niewielka, proces może być mniej efektywny i wymagać dłuższego czasu pracy. Ponadto niektóre substancje mogą ulegać degradacji pod wpływem wysokich temperatur, co ogranicza ich zastosowanie w tym procesie.
Jakie są kluczowe czynniki wpływające na efektywność destylacji rozpuszczalników
Efektywność destylacji rozpuszczalników zależy od wielu czynników, które mogą znacząco wpłynąć na jakość i wydajność procesu. Jednym z najważniejszych elementów jest temperatura wrzenia poszczególnych składników mieszaniny. Im większa różnica temperatur wrzenia, tym łatwiejsze jest oddzielenie substancji. W przypadku bliskich temperatur wrzenia konieczne może być zastosowanie bardziej zaawansowanych metod, takich jak destylacja frakcyjna, która umożliwia wielokrotne skraplanie i parowanie. Kolejnym istotnym czynnikiem jest ciśnienie, które ma wpływ na temperatury wrzenia cieczy. W niektórych przypadkach obniżenie ciśnienia może umożliwić destylację substancji w niższych temperaturach, co jest korzystne dla termolabilnych związków chemicznych. Również konstrukcja kolumny destylacyjnej oraz jej parametry, takie jak wysokość czy liczba teoretycznych półek, mają kluczowe znaczenie dla efektywności separacji. Odpowiedni dobór materiałów oraz ich właściwości fizyczne również wpływa na przebieg procesu.
Jakie są nowoczesne technologie w destylacji rozpuszczalników
W ostatnich latach rozwój technologii związanych z destylacją rozpuszczalników przyniósł wiele innowacji, które zwiększają efektywność i oszczędność tego procesu. Nowoczesne systemy destylacyjne często wykorzystują automatyzację oraz zaawansowane technologie monitorowania, co pozwala na precyzyjne kontrolowanie warunków operacyjnych. Przykładem mogą być systemy zdalnego monitorowania, które umożliwiają operatorom śledzenie parametrów procesowych w czasie rzeczywistym oraz dostosowywanie ich w razie potrzeby. Ponadto rozwój materiałów kompozytowych i nanotechnologii przyczynił się do powstania bardziej wydajnych kolumn destylacyjnych o lepszych właściwościach separacyjnych. Warto również wspomnieć o zastosowaniu energii odnawialnej w procesach destylacji, co przyczynia się do zmniejszenia kosztów operacyjnych oraz ograniczenia negatywnego wpływu na środowisko. Innowacyjne podejścia obejmują także techniki takie jak destylacja membranowa czy ekstrakcja cieczy z cieczą, które mogą stanowić alternatywę dla tradycyjnych metod destylacyjnych w niektórych zastosowaniach.
Jakie są wyzwania związane z procesem destylacji rozpuszczalników
Mimo wielu zalet, proces destylacji rozpuszczalników wiąże się również z pewnymi wyzwaniami, które mogą wpływać na jego skuteczność i opłacalność. Jednym z głównych problemów jest konieczność ciągłego monitorowania i dostosowywania warunków operacyjnych, co wymaga odpowiedniej wiedzy i doświadczenia personelu obsługującego urządzenia. Dodatkowo niektóre składniki mieszanin mogą tworzyć azeotropowe układy, co utrudnia ich separację i wymaga zastosowania dodatkowych metod lub reagentów do osiągnięcia pożądanej czystości produktu końcowego. Koszty inwestycji w nowoczesne urządzenia oraz ich eksploatację mogą być znaczne, co sprawia, że przed podjęciem decyzji o wdrożeniu technologii warto przeanalizować aspekty ekonomiczne. Problemy związane z bezpieczeństwem pracy również nie mogą być pomijane; wiele rozpuszczalników jest łatwopalnych lub toksycznych, co wymaga zachowania szczególnej ostrożności podczas prowadzenia procesów destylacyjnych.
Jakie są przyszłe kierunki rozwoju technologii destylacji rozpuszczalników
Przyszłość technologii destylacji rozpuszczalników zapowiada się obiecująco dzięki ciągłemu postępowi naukowemu oraz innowacjom technologicznym. Jednym z kluczowych kierunków rozwoju jest dążenie do zwiększenia efektywności energetycznej procesów separacyjnych poprzez zastosowanie nowych materiałów oraz technologii odzysku ciepła. Wprowadzenie inteligentnych systemów zarządzania procesami pozwoli na lepsze dostosowanie parametrów operacyjnych do zmieniających się warunków pracy oraz optymalizację zużycia energii. Również rozwój biotechnologii może przyczynić się do powstania nowych metod separacji opartych na enzymach lub mikroorganizmach, co może stanowić alternatywę dla tradycyjnych procesów chemicznych. Zwiększone zainteresowanie zrównoważonym rozwojem oraz ekologicznymi rozwiązaniami będzie miało wpływ na wybór surowców oraz metod produkcji, co może prowadzić do opracowania bardziej przyjaznych dla środowiska technologii destylacyjnych.
Jakie są różnice między destylacją a innymi metodami separacji
Destylacja to jedna z wielu metod separacji substancji chemicznych, a jej skuteczność często porównuje się z innymi technikami takimi jak ekstrakcja czy chromatografia. Główna różnica między tymi metodami polega na zasadzie działania; podczas gdy destylacja opiera się na różnicy temperatur wrzenia składników mieszaniny, ekstrakcja wykorzystuje różnice w rozpuszczalności substancji w różnych fazach (np. cieczy i gazu) lub w różnych rozpuszczalnikach. Chromatografia natomiast polega na oddzieleniu składników mieszaniny na podstawie ich interakcji z fazą stacjonarną i ruchomą. Każda z tych metod ma swoje zalety i ograniczenia; na przykład ekstrakcja może być bardziej skuteczna w przypadku substancji o podobnych temperaturach wrzenia, ale wymaga odpowiednich rozpuszczalników, które mogą być drogie lub toksyczne. Chromatografia oferuje wysoką selektywność i czystość produktów końcowych, ale może być kosztowna i czasochłonna w porównaniu do tradycyjnej destylacji.
Jakie są najczęściej stosowane materiały w kolumnach destylacyjnych
W kontekście budowy kolumn destylacyjnych kluczowym aspektem jest dobór odpowiednich materiałów, które zapewnią wysoką wydajność procesu separacji oraz trwałość konstrukcji. Najczęściej stosowanymi materiałami są stal nierdzewna oraz szkło; stal nierdzewna charakteryzuje się dużą odpornością na korozję i uszkodzenia mechaniczne, co sprawia, że jest idealnym wyborem dla przemysłowych instalacji destylacyjnych. Szkło natomiast pozwala na łatwe monitorowanie przebiegu procesu oraz identyfikację ewentualnych problemów bez konieczności demontażu urządzeń. W przypadku bardziej zaawansowanych technologii wykorzystywane są także materiały kompozytowe czy ceramika o wysokiej odporności chemicznej i termicznej. Dodatkowo istotnym elementem kolumny są wypełnienia; materiały te mają za zadanie zwiększyć powierzchnię kontaktu między fazami gazową a ciekłą, co sprzyja efektywniejszej separacji składników mieszaniny.