Destylator przemysłowy to urządzenie służące do separacji składników cieczy na podstawie różnic w ich temperaturach wrzenia. Proces ten jest kluczowy w wielu branżach, w tym w przemyśle chemicznym, petrochemicznym oraz spożywczym. Destylacja polega na podgrzewaniu cieczy do momentu, gdy zaczyna parować, a następnie schładzaniu pary, aby uzyskać czystą substancję w postaci cieczy. W przypadku destylatorów przemysłowych często stosuje się kolumny destylacyjne, które zwiększają efektywność procesu poprzez wielokrotne skraplanie i parowanie. Dzięki temu możliwe jest uzyskanie wysokiej czystości produktów końcowych. Warto zaznaczyć, że destylatory przemysłowe mogą być wykorzystywane do produkcji alkoholu, oczyszczania wody czy też wydobywania olejków eterycznych.
Jakie są rodzaje destylatorów przemysłowych i ich zastosowania
W przemyśle wyróżnia się kilka typów destylatorów, które różnią się zarówno budową, jak i zastosowaniem. Najpopularniejsze z nich to destylatory prostokątne oraz kolumnowe. Destylatory prostokątne są najczęściej używane w małych zakładach produkcyjnych i laboratoriach, gdzie proces destylacji jest mniej skomplikowany. Z kolei kolumnowe destylatory charakteryzują się większą efektywnością i są stosowane w dużych zakładach przemysłowych. Innym rodzajem są destylatory frakcyjne, które umożliwiają oddzielanie kilku składników jednocześnie na podstawie ich temperatur wrzenia. W przemyśle chemicznym wykorzystuje się również destylatory próżniowe, które działają w obniżonym ciśnieniu, co pozwala na destylację substancji o wysokiej temperaturze wrzenia bez ich rozkładu.
Jakie są kluczowe elementy konstrukcyjne destylatora przemysłowego
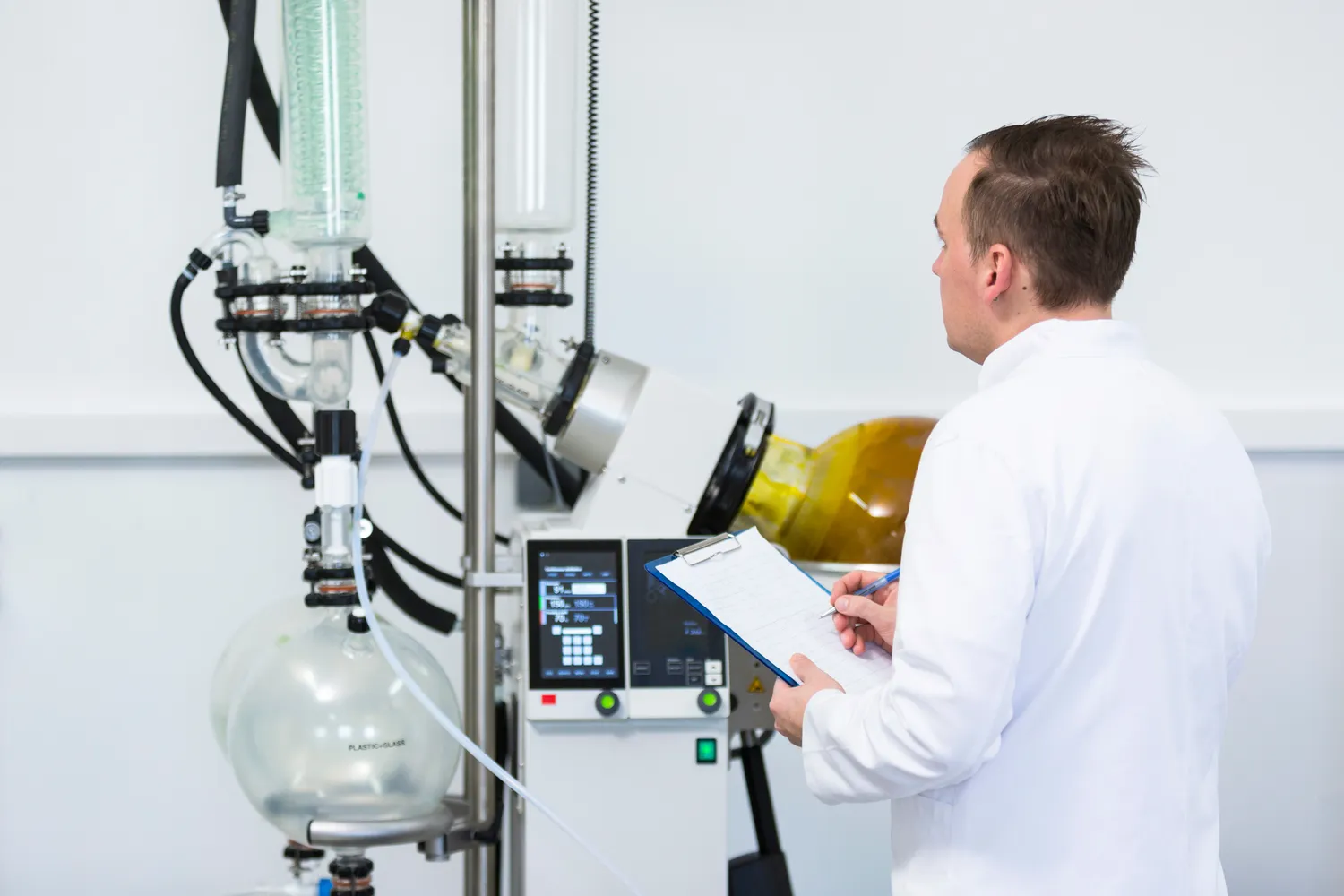
Konstrukcja destylatora przemysłowego składa się z kilku kluczowych elementów, które mają istotny wpływ na jego wydajność oraz efektywność działania. Podstawowym elementem jest zbiornik na ciecz surową, który umożliwia podgrzewanie materiału do odpowiedniej temperatury. W górnej części destylatora znajduje się kondensator, który schładza parę i przekształca ją z powrotem w ciecz. Ważnym komponentem jest także kolumna destylacyjna, która może być wyposażona w różne elementy wspomagające separację składników, takie jak packingi czy talerze. Dodatkowo niezbędne są systemy kontroli temperatury oraz ciśnienia, które zapewniają optymalne warunki pracy urządzenia. Warto również zwrócić uwagę na systemy odprowadzania odpadów oraz recyklingu substancji chemicznych, co jest istotne z punktu widzenia ochrony środowiska oraz efektywności ekonomicznej procesu.
Jakie są korzyści z używania nowoczesnych destylatorów przemysłowych
Nowoczesne destylatory przemysłowe oferują szereg korzyści, które mogą znacząco wpłynąć na efektywność produkcji oraz jakość uzyskiwanych produktów. Przede wszystkim nowoczesne technologie pozwalają na zwiększenie wydajności procesu destylacji poprzez zastosowanie zaawansowanych systemów automatyzacji oraz monitorowania. Dzięki temu możliwe jest precyzyjne kontrolowanie parametrów pracy urządzenia, co przekłada się na lepszą jakość końcowego produktu oraz mniejsze straty surowców. Ponadto nowoczesne destylatory często charakteryzują się mniejszym zużyciem energii dzięki innowacyjnym rozwiązaniom konstrukcyjnym oraz materiałowym. Wiele z nich jest także zaprojektowanych z myślą o minimalizacji wpływu na środowisko naturalne poprzez zmniejszenie emisji szkodliwych substancji oraz efektywniejsze zarządzanie odpadami.
Jakie są najczęstsze problemy związane z destylatorami przemysłowymi
Podczas eksploatacji destylatorów przemysłowych mogą występować różne problemy, które mogą wpływać na efektywność procesu oraz jakość uzyskiwanych produktów. Jednym z najczęściej spotykanych problemów jest zatykanie kolumny destylacyjnej, co może prowadzić do obniżenia wydajności oraz jakości destylacji. Zatykanie może być spowodowane osadzaniem się substancji stałych lub cieczy o wysokiej lepkości, co wymaga regularnego czyszczenia i konserwacji urządzenia. Innym problemem jest niewłaściwe ustawienie parametrów pracy, takich jak temperatura czy ciśnienie, co może prowadzić do nieefektywnej separacji składników. W przypadku destylatorów frakcyjnych, niewłaściwe dobieranie wysokości kolumny lub liczby talerzy może skutkować nieodpowiednim rozdziałem substancji. Dodatkowo, awarie systemów chłodzenia mogą prowadzić do przegrzania urządzenia, co z kolei może skutkować uszkodzeniem sprzętu oraz stratami materiałowymi.
Jakie są koszty związane z zakupem i eksploatacją destylatora przemysłowego
Koszty związane z zakupem i eksploatacją destylatora przemysłowego mogą być znaczne i powinny być dokładnie przemyślane przed podjęciem decyzji o inwestycji. Cena zakupu destylatora zależy od jego typu, wielkości oraz zastosowanych technologii. Proste destylatory prostokątne mogą kosztować kilka tysięcy złotych, podczas gdy zaawansowane kolumnowe destylatory frakcyjne mogą sięgać setek tysięcy złotych. Oprócz kosztów zakupu należy również uwzględnić wydatki związane z instalacją oraz uruchomieniem urządzenia, które mogą być znaczące w przypadku skomplikowanych systemów. Koszty eksploatacji obejmują zużycie energii, konserwację oraz ewentualne naprawy. Warto również pamiętać o kosztach surowców oraz odpadów, które powstają w wyniku procesu destylacji.
Jakie są najnowsze trendy w technologii destylacji przemysłowej
W ostatnich latach można zaobserwować wiele innowacji w dziedzinie technologii destylacji przemysłowej, które mają na celu zwiększenie efektywności procesów oraz minimalizację wpływu na środowisko. Jednym z najważniejszych trendów jest automatyzacja procesów destylacyjnych, która pozwala na precyzyjne monitorowanie i kontrolowanie parametrów pracy urządzeń. Dzięki zastosowaniu nowoczesnych systemów informatycznych możliwe jest zbieranie danych w czasie rzeczywistym oraz ich analiza, co przekłada się na lepszą jakość produktów oraz mniejsze straty surowców. Kolejnym istotnym trendem jest rozwój technologii odzysku ciepła, która pozwala na wykorzystanie energii cieplnej generowanej podczas procesu destylacji do podgrzewania surowców lub wody użytkowej. Tego rodzaju rozwiązania przyczyniają się do zmniejszenia zużycia energii i obniżenia kosztów operacyjnych.
Jakie są wymagania dotyczące bezpieczeństwa w pracy z destylatorami przemysłowymi
Praca z destylatorami przemysłowymi wiąże się z pewnymi zagrożeniami, dlatego niezwykle ważne jest przestrzeganie odpowiednich norm i przepisów dotyczących bezpieczeństwa. Przede wszystkim należy zapewnić odpowiednią wentylację pomieszczeń, w których znajdują się urządzenia, aby uniknąć gromadzenia się szkodliwych oparów chemicznych. Wszyscy pracownicy powinni być przeszkoleni w zakresie obsługi urządzeń oraz zasad BHP, aby minimalizować ryzyko wypadków. Ważnym aspektem jest także stosowanie odpowiednich środków ochrony osobistej, takich jak rękawice czy okulary ochronne. Należy również regularnie przeprowadzać kontrole techniczne urządzeń oraz systemów zabezpieczeń, aby upewnić się, że działają one prawidłowo. W przypadku awarii lub nieprawidłowości konieczne jest natychmiastowe podejmowanie działań naprawczych oraz informowanie odpowiednich służb ratunkowych.
Jakie są kluczowe czynniki wpływające na wybór odpowiedniego destylatora przemysłowego
Wybór odpowiedniego destylatora przemysłowego to decyzja strategiczna, która powinna być oparta na kilku kluczowych czynnikach. Przede wszystkim należy określić rodzaj substancji, które będą poddawane procesowi destylacji oraz ich właściwości fizykochemiczne. Różne substancje wymagają różnych typów urządzeń i technologii, dlatego ważne jest dokładne zrozumienie specyfiki procesu produkcji. Kolejnym czynnikiem jest wydajność urządzenia – im większa wydajność, tym bardziej opłacalna produkcja. Należy również zwrócić uwagę na koszty eksploatacji i konserwacji urządzenia oraz dostępność części zamiennych i serwisu technicznego. Warto także rozważyć aspekty ekologiczne związane z wyborem konkretnego modelu – nowoczesne technologie często oferują lepsze rozwiązania pod względem efektywności energetycznej i minimalizacji odpadów.
Jakie są najlepsze praktyki dotyczące konserwacji destylatorów przemysłowych
Aby zapewnić długotrwałe i efektywne działanie destylatorów przemysłowych, niezwykle istotna jest regularna konserwacja urządzeń. Kluczowym elementem jest tworzenie harmonogramu przeglądów technicznych oraz czyszczenia poszczególnych komponentów systemu. Regularne sprawdzanie stanu kolumny destylacyjnej pozwala na wykrycie ewentualnych osadów czy zanieczyszczeń zanim staną się one poważnym problemem. Ważne jest także monitorowanie parametrów pracy urządzenia – wszelkie odchylenia od normy powinny być natychmiast analizowane i korygowane. Dobrą praktyką jest także dokumentowanie wszystkich działań konserwacyjnych oraz wyników przeglądów technicznych, co ułatwia późniejsze analizy i identyfikację potencjalnych problemów.
Jakie są przyszłościowe kierunki rozwoju technologii destylacji przemysłowej
Przemysłowa technologia destylacji znajduje się w ciągłym procesie innowacji i rozwoju, a przyszłość tej branży zapowiada się obiecująco dzięki wielu nowym kierunkom badawczym i technologicznym. Jednym z najważniejszych trendów jest rozwój inteligentnych systemów zarządzania procesami produkcyjnymi opartych na sztucznej inteligencji i uczeniu maszynowym. Takie rozwiązania umożliwią optymalizację procesów w czasie rzeczywistym poprzez analizę danych zbieranych przez czujniki umieszczone w urządzeniach. Kolejnym kierunkiem rozwoju jest integracja technologii odnawialnych źródeł energii w procesach produkcyjnych, co pozwoli na zmniejszenie śladu węglowego i zwiększenie efektywności energetycznej zakładów produkcyjnych.